Raw Materials for Blocks Production
The most common and popular raw materials adopted by our customers as below:
Sand, Cement, Slag, gravel, stone powder, fly ash, gangue, industrial waste, water and so on. However, all kinds of popular and customized blocks can be produced by mixing the raw material, and the most popular blocks are hollow blocks, porouse blocks, interlocking block, solid blocks, curbstone, paving blocks, etc. In addition to, the colorful blocks can be also manufactured by adding our patented dye machines.
Just contact us, and the block machines will be designed and produced for your specific and special block production request.
Production Process of the Block Machines
The production process of the block machine: welding, cutting, assembling, polishing, measuring and wiring
Solutions of Block Making Machine
Raw Material and Precessing of Linghao Block Machine:
Linghao Block Making Machine is maded of Q235B high quality carbon structural steel and Q345B high quality low alloy steel, and dealt with professional heat treatment process, so that the block making mahcine is strong enough and durable even for 10+ years.
For example:The structural parts are made of Q235B high-quality carbon structural steel, the wear-resistant parts are made of Q345B high-quality low-alloy steel, the casting parts are made of HT200 gray cast iron, the vibration box and other important casting parts are made of ZG350-500H special casting steel, gears 20CrMnTi high-quality carburized steel is used for similar components, and 45# high-quality carbon structural steel is used for shaft transmission components and vibration core components.
Heat Treament Process: Professional heat treatment technology and processing methods are used to optimize mechanical properties, so that the block machine can work even 10+ years.
Cutting Process:
According to the processing requirements of finished products, it can be divided into laser cutting, flame cutting, plasma cutting, sawing, turning, milling, grinding, boring, drilling, etc.
Why the Block Machine is Needed?
In fact, the block machines are absolutely necessary for the block production industry.
First, the block machines are more efficient than the production by workforce. As per the rapid requests of constrution, buildings, more blocks are required and it is an inevitable demand. So we need the block machines, especially the high quality and reliable suitable block machines.
Secondly, more and more customized blocks including special sizes, shapes or materials are needed. It is impossible to satisfy the requests without the block machines. After all, only common blocks can be produced by workers.
Thirdly, variouse types of blocks such as hollow blocks, porous blocks, interlocking block, solid blocks, curbstone, paving blocks and other blocks are needed, and the reliable blocks produciton line will meet the diversified needs perfectly.
Finally, quality blocks are becoming more and more important, since the buildings depend on the quality of blocks a lot. With hydraulic system, PLC automatic control system, and strong pressure, the perfect blocks will be made then.
In one word, the block making machines are needed, and the customers are advised to choose reilable, professional and excellent block machines.
Models of Linghao Block Making Machine
The block machines can be classified as per raw material, automiatic or not, and shapes.
When it refers to automatic or not, our block machines include automatic block machines, semi automatic block machines, manual block machines.
The manual block machines is very fit for block workshop,the semi automatic block machines is adopted by newer, small and medium factory of block, and the automatic block machines are bought by medium and large block production factory.
The most popular blocks machines are: QT4-26,QT4-25,QT4-15,QT5-15,QT6-15,QT8-15,QT10-15,QT12-15,QT15-15,JMQ-4A,JMQ-6A,JMQ-10A,JMQ-12A.
In addition to, the automactic block machine will make better quality blocks than the semi automatic and manual block machine, because all the production process is controlled by PLC control system , and guarantee the batching, mixing, vibrating, pressing, moulding, curing proecess perfectly, then the pefect blocks are produced by the automatic block machine.
As for the raw materials, the block machines include: concrete block machine, cement block machine, fly ash block machine,clay block machine,cinder block machine, etc. Fortunately, Our block machines can produce blocks with all the materials.
The block machines include hollow block machine, interlocking block machine, paving block machines, solid block machine, curbstone block machine,etc. Of course, our block machines can produce all different sizes and shapes blocks, and we will also supply customized mould so that the block machine can satisfy your customized requests.
90% of our customers bought the block machines above.
Fomula for Blocks Production
The quality of the blokcs is decided by the raw material fomula, the block machines and production process. The raw material ratio will come first.
The raw material fomula from our customers for reference: different fomula will be adopted for different customers, and customers are requested to determine a reasonable mix ratio based on actual conditions of the factory.
A: Concrete Blocks:
B: Hydrated Lime Fly Ash Bricks – Steam Curing Proceeding
What is Lime Hydration?
Lime Hydration: The lime will hydrolyze after it meets water, produce calcium hydroxide, release heat, and expand the volume by 2-3 times. This process is called quicklime digestion.
C:Fly Ash Bricks with Cement – Natural Curing Proceeding
In this case, the materials would be primarily focused on cement rather than on gypsum and lime.
D:The Others Formula for Fly Ash Bricks
Gypsum: Gypsum plays a role in accelerating hydration reaction, increasing crystallization of hydrates, and improving the early strength of bricks, especially the flexural strength, in the production of autoclaved fly ash.
Fly Bricks with 2% Gypsum-Autoclave Steam Curing Proceeding
Fly Bricks with 1% Gypsum-Autoclave Steam Curing Proceeding
E: Burned Fly Ash Bricks with clay or soil
F:The materials or ingredients needed here are Gypsum, Sludge Lime, Fly Ash, and Sand/Stone Dust.
The raw materials for making blocks: Sand, Cement, Slag,gravel, stone powder, fly ash, gangue, industrial waste, water and so on.
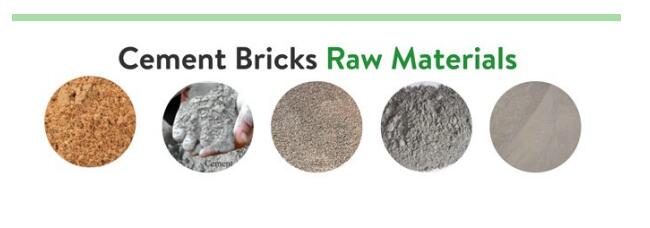
Take concrete hollow blocks and porous cement for example, the material and ratio will be as below:
Size: 390mm*190mm*190mm First Level blocks
Raw Material:
Cement:12 bags
Fly Ash:4 shovels
Medium Sand: 24 shovels
Gravel: 54 shovels
Stone Powder: 84 shovels
Water: 0.3%-0.4%
The Strength: MU10
Size: 390mm*190mm*190mm First Level blocks
Raw Material:
Cement: 8 bags
Fly Ash: 50 shovels
Medium Sand: 7 shovels
Gravel: 35 shovels
Stone Powder: 42 shovels
Water: 0.3%-0.4%
The Strength: MU5
How Does the Block Machine System Work?
The block making system will work perfectly with the machines as below: Concrete Batching Plant, Pallet Feeding System, Block Making Machine, Block Stacker System, Controlling System, and other machines.
Concrete Batching Plant includes: PLD Batching Machine, Concrete Mixer, Belt Conveyor, Cement Silo, Cement Screw Conveyor, Weighing System
Pallet Feeding System: Pallet Feeder, Dye Machine
Block Machine: Automatic, Semi Automatic and Manual Host Block Machine
Block Stacker System: Block Stacker
Controlling System: PLC Control System, Hydraulic Station
Other machines:Forklift, Loader, Finished Block Transfer Cart
Spare Parts: Block Pallet, Block Mould, Steel Protection Structure
We prefer to share more about the machines:
Concrete Batching Plant: It is the raw material supplying system, all the materials will be mixed and supplied to the block machines. The cement silo is the device for storing the cement, and the cement screw conveyor is adopted to transfer the cement, and the weighing system is used for water weighing, cement weighing and aggregate weighing.
With the concrete batching plant, the raw materials can be mixed and supplied with accurate material ratio to block machine.
Block Making Machine: The raw materials supplied by the concrete batching plant will be vibrating, pressing, moulding and curing carefully. It is the main machine of the block making system
Pallet Feeding Sytem:
It is the system to supply the pallet to the block making machine. The finished block from the block machine will be loaded by the pallet supplied by pallet feeding system.
Block Stacking System:
The system is adopted to stack the pallet with finished block. The system includes common stacker and the absolutely smart automatic multi-function stacking system.
Controlling System: The PLC controller let the concrete batching plant, the block machine, pallet feeder and block stacker run automatically and smoothly.
Other Machines: The loader is used to put the aggregate material to batching machine, the forklift and finished block transfer cart are adopted to deliver the pallets with finished blocks efficiently.
Spare Parts: The block mould is the important part of block machine, and can produce different and customized shape blocks. The block pallet includes plastic pallet and GMT pallet, and 99% of the customers adopt GMT pallets for its cost-effective and long life-time.
How to Maintain Block Making Machine and Finished Blocks?
To ensure the longevity of the block making machine:
1.Please be sure the block machine is operated by experienced and trained workers. The workers are familiar with the block machines, understand the functions of the machine, and will stop the machine in time if some problems occurred.
2.Please kindly read the operation manual and maintaining instructions. And please maintain the block machines regularly.
3.Please assure the block machine keeps low temperature. Low temperature will keep the machine run perfectly and efficiently, and will also keep the parts from broken for high temperature.
4.Please clear the block machine, including grease and wastes in the cavity and out of the surface of the machine mold.
5.Please check the block machine regularly, including but not limited to check the damaged parts, loose parts, etc.
In fact, the maintain process will take some time and a little money, but it is very very valuable. As you know, much more money and much more time will be spent to repair the block machine, if the block machines come across problems, so why not spend less time and money to maintain the machine?
A Brief Guide to Maintaining Your Concrete Blocks
1.Please be patient to wait the block become strong enough, after the blocks are transported to the site
2.The water is not required for the first day, because the concrete is easily lost for the first day.
It is very important to keep mositure of the blocks for the first day. For example, straw curtains and plastic can be adopted.
3.The block slabs should be seperated and stacked, when the blocks become strong enough. Then watering maintenance of the blocks should come.
4.The important thing is to keep moisture of the block. Generally speaking, about 3 times watering maintenance needed in next 6-9 days.
5.The strength of the block will be about 70% strong enough and can be sold.
How to Open A Block Production Factory?
How to begin the block factory:
There are some factors have to consider, when you’re planned to set up a block factory.
1.It will be great if you can communicate with your government, and familiar with the policy and regulations. You also need to get the license and permission from your government.
2.Detailed business plan should be worked out. You need to investigate the market, factory production plan,the expected profit and approximate cost, etc.
3.You need to apply for the land, the land should be ok enough for the raw material storing, the block machines plant, the block mataining site, facility site, office, etc.
In addtion to, the land couldn’t be a swampy, and the land should be near the water resource,and rich in raw materials.
4.Buy the reliable block making machine. You’re welcome to contact my factory, and we will advise the fit block making machine as per the capacity you want, the approxiamte size of your plant, etc.
As you know, the quality of blocks are related to the formula of raw materials, block machines and production process.
If the machine always shuts down, you cannot achieve your capacity expectation and quality request, so contact us and get the right block machines and professional advices.
5.Confirm the stable supply of cement. To be honest, the cement is the priority of raw materials, it will be great if the cement can be stored in the cement silo.
Confirm the pigment supply, if you want to produce the colored blocks.
6.Buy or rent the auxiliary such as loader, forklift, power generator, crushing machine, as well as packaging machine, etc.
7.Employ the workers and train them. The experienced and reliable customers will make the block machines run more smoothly.
Capacity of Our Block Making Machines:
As for the automatic block machine: 960pcs-130000 pcs per 8 hours
As for the semi automatic block machine: 590pcs-2600pcs per 8 hours
As for mobile block machine: 300pcs-2500pcs per 8 hours
All the capacity is approximate, and for some certain blocks. The accurate capacity can be worked out if the specific size and shape of blocks are shown.
Popular Types of Finished Blocks?
Types of blocks by materials:
The cement blocks, concrete blocks, cinder blocks, fly ash block, clay blocks, etc.
The most popular and main blocks are concrete blocks:
1.the concrete blocks are strongest and very fit for the buildings and construction industry.
2.The concrete blocks can be produced by machines, so the production is very very high efficient
3.The concrete blocks are profitable, as per the production cost and sales price.
4.There is very professional and world wide supplying system for the raw materials especially concrete. It means, the raw materials can be easily got in low price.
Types of blocks by shapes:
1.Hollow Blocks
2.Solid Blocks
3.Paving Blocks
4.Curbstons Blocks
5.Interlocking Blocks.
The most popular blocks are hollow blocks, because it is adopted in many applications, and also the hollow blocks will cost less materials. It means, more profit will be made.
Sizes of the blocks:
The sizes of the blocks depend on the mould and the shapes of the blocks. The weight of the blocks (that is critical for the consumption of raw material) will be affected by both the sizes and shapes of the blocks.
Most popular size of blocks:
Hollow blocks: 400*200*200mm; 390*190*190; 390*150*190, etc.
Porous blocks: 240*115*90mm; 240*200*90mm; 240*115*53mm, etc.
Solid blocks: 240mm*115mm*53mm, 200*100*60mm,etc.
Paving blocks: 225mm*112.5mm*60mm, 250*250*60mm; 200*160*60mm; 200*100*60mm, etc.
Advantages of Linghao Block Machines
1.Absolutely Low Production Cost: With 30+ years production experienced factory, we’re professional enough in every points of the products, and we know how to produce the excellent block machines with lowest cost. In addtion to, we have long term secondary supplier of steel and parts.
With all these advantages, we can reduce the productions cost maximize and will save more for the customers.
Of course, the price is absolutely different, as per different quality block machines. What you have to consider is if the block machine is cost-effective, and if the block machine values the money you paid.
2.Reliable Raw Material: Q235 steel is adoped to produce the block machine, so you can trust our block machines.
3.Siemens and ABB Motor, Omron and Schneider Electric Parts, Japan Yuken PLC controller, Taian Hydraulic System adopted, so that block machine can run perfectly.
4.Certificate:CE and ISO certificate is available, and we can also let our block machines tested for your special certificate.
5. Production in time and delivery professionally:
With 360 sets of prdocution machines, and 600 workers,we produce 10000+ sets machines for customers in time every year. We can deliver the block machines in 30 days.
With more than 30+ Chinese First Forwarders and International Forwarders, we have delivered the block machines to our customers fast and smoothly.
6.Considerable After-sales Service:
With 30+ years experience, we’re familiar enough with the block machines, as well as the frequent problems, customers’ request. So it is no doubt that we can supply the professional and considerate after-sale service.
How to Choose the Right Block Machines?
When you start to choose the block machines, please kindly consider below:
1.Reasonable price of the block machines
2.The after-sale service is available
3.The timely production and professional delivery
4.The raw material control system and Q/C before the block machines delivered
5.The PLC, the motors, electric parts should be brand and reliable
6.The block machines should be reliable and high efficient
7.Pls kindly work out your request, including the blocks application, the budget, the raw material, etc. Then choose the most suitable block machines as per the requests.
8.It will be great if the block machine is eco and environment-friendly
9.The installtion service, maintenance service, technical support, the spare parts have to be available
10.The auxilry machines should be available, that is, the one-stop factory should be chosen.
11.It will be perfect if the block machines run very silently.
How to Install the Block Molding Machine?
Fortunately, you don’t have to fret about installation since we will provide videos. Alternatively, we can send our engineers to help you go about it.
In addition to installation, the engineer will train your operator and ensure everything is working properly.
However, ensure that the machine has all the essential parts such as block stacker, hydraulic station, PLC control system, host machine, concrete mixture, and batch bin.
Next, ensure that the voltage is tailored to match that of your country to avoid machine damage.
Once the engineer installs the machine, you can go ahead and test it. If in the future you get stuck, you can always reach us for guidance.
Price of Linghao Block Making Machine
We understand that you want to get the reliable block machines, with lowest price. It is normal and wise.
However, the price of the block machines will be decided by the raw material, the parts, the control system, the durability, the factory’s experience, after-sale service, etc. So the price is valuable by considering the factors, rather the price is low so I choose it.
Generally speaking, the price of our block machines will be USD2350-USD133350,EXW.
Just contact us, and you will get the valuable price of our block machines.
The Block Making Machines Make Money, Is It Profitable?
To answer the questions, we can consider as below:
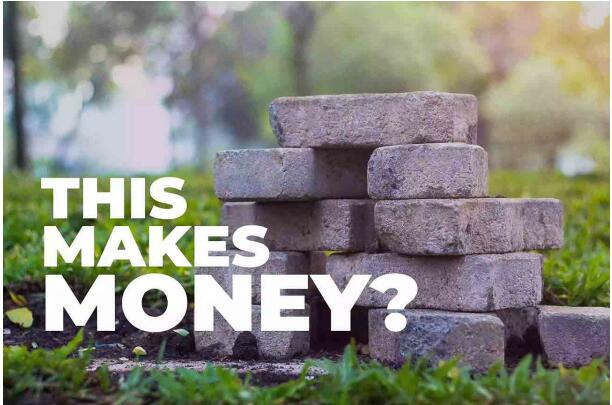
First, the market requests the block machines:
the block is required by the construstion industry and buildings, it is necessary for the development of the countries. So the block making machines are needed, of course.
Second, how about the cost and profit from the customers:
As per the reply from our customers, the block macine cost and the raw material cost, as well as the other cost are acceptable, the profit will be about 10%-15%. The investment will be made up about 13 months, then the customers will make money by the block machines.
Thirdly, the raw material supplying system:
The most common and popular raw material adopted by our customers as below:
Sand, Cement, Slag, gravel, stone powder, fly ash, gangue, industrial waste, water and so on. And all the materials are very very easy to get any where. So the raw materials should never be a problem.
Finally, are you professional enough:
You have to investigate the block market, so that the perfect and practical plan can be worked out.
However, we will help you and supply professional advice.
Generally speaking, 95% of our customers get the investment 11 months to 13 months, then will make profit 15% per year.
How To Choose The Concrete Block Mold?
The mould is very important parts of the block machine, and it will affect the quality and shapes of the final blocks.
Concrete Block Mould Advantages:
1.Electric wire cutting technology adopted, and the thick steel plate will be cutted as the whole for perfect strength. And the finished mould is high precision and durable even for 10 years.
2. Carburizing heat treatment process is used, and the strength and troughness of the mould is guaranteed.
3. Raw material: High manganese steel, it will make it possible to make even more durable mould.
Block Mould With Wire Cutting Technology
Block Mould After Heat Treatment
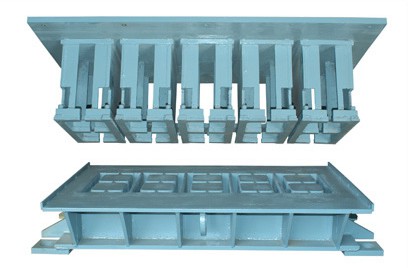
Concrete Hollow Block Mould”
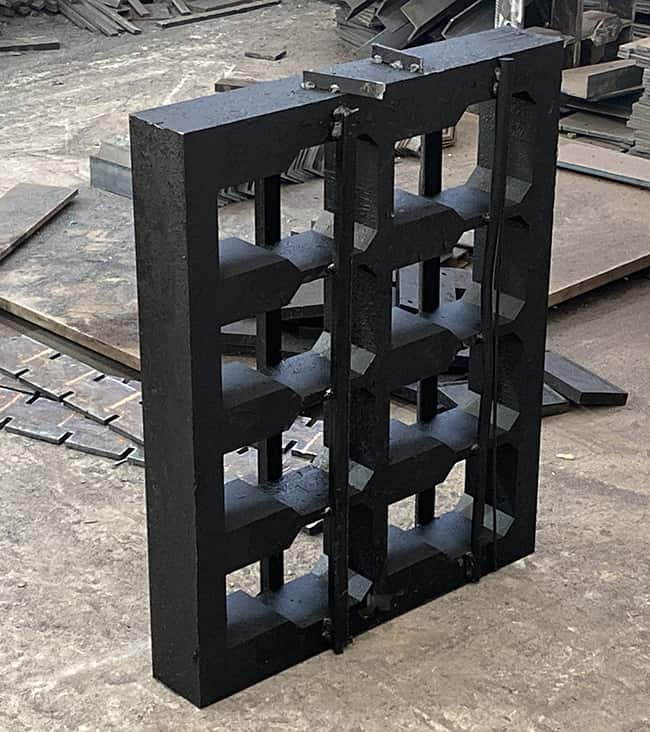
Concrete Interlocking Mould”
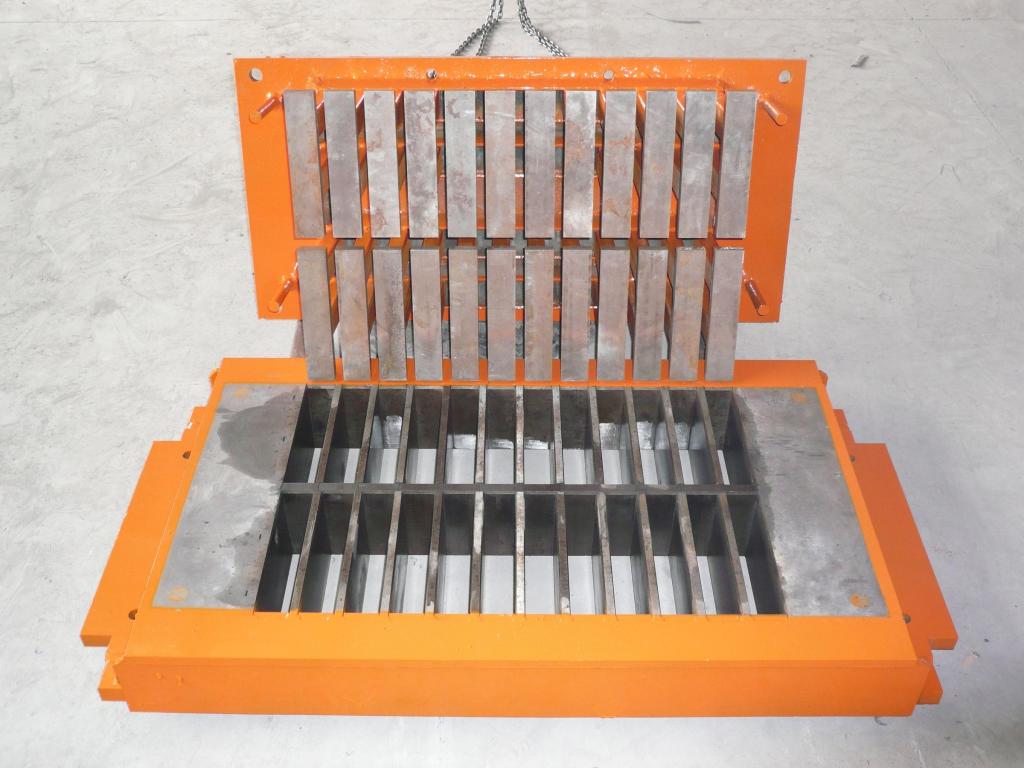
“Concrete Solid Block Mould”
How Does A Hydraulic Brick Making Machine Operate?
The feeding of raw material:
The raw material will be feeded to the block making machine by the raw material system.
Mixing:
the feeded raw materials are mixed, and then passed through raw materials by a belt conveyor
Vibrating and Brick Forming:
The blocks are formed by vibration and hydraulic pressure. Of course the block pallet should be feeded by pallet feeder.
Molding
Once the mixture attains the required proportion, a conveyer belt moves it to a hopper, which then drains it into the mold. The mold contains inner molds that determine the shape and size of the bricks. Through hydraulic pressure and vibration, the bricks are produced within seconds. The pressure cylinders push the bricks down to a waiting pallet that is pushed to a chain belt that leads to a waiting manual cart.
Curing
Curing takes place in a curing kiln. Here, there can be more than 100 bricks at a go. The most commonly used kiln is a steam model. The bricks are held for at least three hours and then steam at regulated temperature is introduced. After they soak up enough moisture, removal of the moist air begins as temperature levels rise to harden the bricks.
Cubing
This process involves packaging the bricks in cubes for easy storage.
CE, CO, FORM, SGS, GOST Certificates are Available.
QT4-25, QT4-26,QT5-15,QT6-15,QT8-15,QT10-15,QT12-15 Block Making Machine Operation Manual
Why GMT Pallets, rather than PVC or other Material Pallets?
1.Lighter Weight: The GMT density is only 1.2g/cm³, and PVC 1.75g-1.8g/cm³. GMT is about 33% Lighter than PVC with the same size.
2.Longer Life Time: Generally speaking, the GMT pallets can be used for more than 10 years, and PVC or other material pallets are only about 3-4 years.
3.More Stronger and Higher Loading Capacity: The GMT pallets are lower flexure, compared to PVC or other material pallets.
4.Abrasion Resistant: There will be absolutely no abrasion for GMT pallets.
5.Higher Impact Resistant: Impact resistant of GMT pallets is 30KJ/m³, and PVC pallets is only 15KJ/m³. And rhe impact resistance of GMT pallets is 2 Times of PVC pallets in same conditions.
6.Better Water Proof: The water absorption rate is <1% for GMT pallets, and it is perfect for finished blocks.
Switch, Reducer, Bearing, Chains, etc.